私が貴重な経験を積むことが出来たのは、自分自身が持つ好奇心旺盛な性格と強運に恵まれた結果思っている。15
歳(現在で考えると高校1年生)で機械、溶接、塗装、板金、自動車整備の基礎を(学科&実技)を学び、実際の自動車製造ラインで艤装、最終検査、アライメント調整、ライト光軸調整、雨漏りテスト&修理、車体製造等を一般社員と一緒に作業をすることにより自然と技術を習得することができた。その後も修理工場、ディラー勤務(横浜日産モーター)も2年間経験した。
@ |
A |
B |
C |
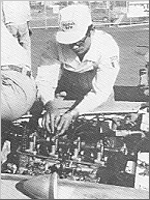 |
 |
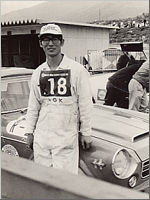 |
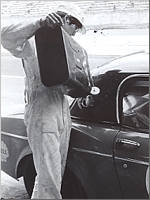 |
@:SR311フェアレディのU20エンジン・タペット調整中の藤沢
A:中央が藤沢。人で隠されて見えないが車両はセドリック・ストックカー
B:22〜23歳頃 SR311
C:携行缶でガソリン給油中の藤沢 富士スピードウェイ・ピット前 |
日産自動車大森分室では、レース車改造開発、レースエンジン改造開発、日産レーシングスクールスタッフ、レースサービス、ラリーサービス、オプション部品開発&製造、試作車製作と多岐に渡って技術を磨くことになる。
部署柄、ほとんどの業務が社外秘事項に該当していたので、あまり公に出来ないことばかりであるが、約30年も経過したので少しだけ公開してみよう。パルサーエクサというクサビ型のFF車が存在したことを知っている人は少ないと思われるが、あのFFエクサのフロントエンジンをミッドシップ(実際はRRに近い)にするというプロジェクトが持ち上がり、私に改造が依頼された。私は1枚の設計図も引かないで1ヶ月ほどでミッドシップ(厳密にはRR車に近い)車を完成させた。トランク部を切開し、エンジンブラケット製作、シフトリンケージ製作、アクセルリンケージ製作、冷却系配管など初めてのトライに熱中し製作を楽しんだ。
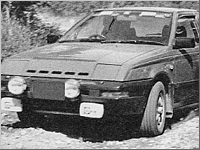 |
クサビ形状のデザインが個性的だったパルサーエクサ。FF方式が出始めた頃。 |
一番苦労したのがエンジン搭載位置の決定である。ガランと開いたスペースに(ボディチェーンブロックで持ち上がっている状態)エンジン、ミション、ドライブシャフト、ストラット、タイヤを取り付けたアッセンブリーを押し込む。ボディの中心線と合わせなければいけないが図面上では中心線が引けても実物車両の中心線など簡単に解らない。エンジンだって中心線など解らない。タイヤだってストラット上部が固定されて始めて向きが解かるわけだから、ブラブラの状態ではアライメントなど測定不可能。更にエンジン位置の上下も決定しなければならないことになる。(実際はエンジン重量で車両は沈み込むことになる)この状態でエンジンブラケットを手作りで製作しなければばらないのでとても難しい作業となる。本来は位置出し治具などを製作して位置決めを実施する。また半年から数年間の開発期間と莫大な開発資金を必要とする作業なのである。今から考えても奇跡的に思えるほど短期間な製作日数と最小限の費用(ありあわせの部品を最大限利用した)で製作したので、今考えても実に感慨深い。エンジンをトランク側に移動したため追いやられたガソリンタンクはフロント側に移設した。もちろん前後重量配分を考慮すれば必然的な結果で収まる位置だ。
この改造に至るまで色々な経験を重ねて技術を蓄積していたことと、他にも、サニー、チェリー、ブルーバード、スカイライン、フェアレデイSR311,セドリックストックカー、フェアレディZ432、フェアレディ240ZなどのTS車両の改造及びラリー車の改造なども手がけてきたので、技術的にはそれほど困難ではなかった。完成した車両で富士スピードウェイの初試験走行のハンドルを、私自らが握り感激しながら軽くフィーリングと不具合をチェック。テスト走行は星野選手が担当した。その結果などは当然ながら社外秘であるため公開できないのが残念である。その後、車両はテクニカルセンターに持ち込まれ、操縦安定性テストが行われたと伝え聞いたのは、だいぶ後になってからのことである。
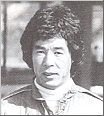 |
当時、2輪で活躍中の若手選手を3名富士スピードウェイでテストを実施する。
星野選手と本橋選手と2名が合格した。 |
その後フロントにもエンジンを載せたツインエンジンのテストに発展してゆく。最近ホンダレジェンドが4WD(駆動力四輪自動配分)を世に出してきたが、30年前にツインエンジン×4WD車がテスト車とはいえ存在した訳だ。一番の課題は前後エンジン回転数の同調であった。当時はまだビスカスカップリングも開発されていない時代であったので、前後エンジンのアクセル開度の微妙な違い(エンジン回転数の違い)を吸収できるのはタイヤのスリップとクラッチのスリップ(オートマ車であれば逃げ場があったがエクサにはAT設定がなく前後共にMT)しかなかったのでテスト走行を重ねるうちに片側のエンジンが壊れてしまった。今にして思えば当然とも言える事なのだが、可能性を追求した実験も必要であり、私は熱中して仕事に没頭していた。(ダートトライアルのモンスター田嶋選手がスズキカルタスのツインエンジンでダートトライアルを戦っていた頃のことである)私が日産市販車の開発ポストに在籍していたとしたら、4輪駆動配分システムの開発をはるか以前に提案していたかもしれない。
サニーTS1300エンジンを開発してゆくと(当時1300ccで165馬力オーバーの出力を得ていた)インテークバルブ&エキゾーストバルブ直径の大型化は必然であった。最後の熟成はバルブ大型化による重量増を軽減すべく、チタンバルブの採用に至る。後はインテークバルブ直径とエキゾースバルブ直径の組み合わせを1mm単位で変更しバランス(マッチング)を煮詰めることに移行してゆく。当然ながら最終的にINとEXバルブが大きくできる限界点に到達してしまう。技術的に突き詰めてゆくと「せめてインテークバルブがもう1本余計にあれば(今や常識の3バルブの発想)良いのに」と到達する。私が20〜21歳の頃だったから30年以上も前になる。日産大森の中で「3バルブ、3バルブ」と私が叫んでも誰も聞く耳は持たなかった。その頃の日産はご存知のようにS20の名機があり、LZ系の4バルブレース専用エンジンと4バルブが高性能の決め手といった風潮があった。トヨタ2TGの2バルブツインカムは眼中になかった。それから15年以上経過し、世に3バルブが販売開始されるが、日産は他社に遅れをとって一番最後に世に出してくることになる。レースでは極限性能の領域で勝負するので、4バルブは大きな意味を持つが一般道路の要求では、3バルブがコスト対性能のバランスに優れていると今でも思っている。また、カムシャフト作動角を色々とテストしてゆけば誰しもが可変作動角、可変バルブタイミングが出来ないものかと考えるようになる。後はその考えを実践しようと動き出す、社内システムが構築されているか否かであり企業体質が大きく影響してくる。また当時の周辺技術はコンピューター制御技術は開発されていないので、可変バルタイを制御する信頼できる技術は整っていなかった。
ある時、技術員から近藤真彦のマーチシルエットをモーターショーに出品するから「できるだけオーバーな感じで製作しなさい」とたった一言(信じられないかと思うが本当の話。日産自動車では技術職が設けられ、指示書に詳細な仕様が書かれた正式な指示書に沿って、現場技術者が実際の作業を実施するのが正規な方法。後日、1行書かれた簡単な指示書を渡される)の依頼が私に舞い込んだ。いつものように1枚のラフスケッチも設計図も引かずに、製作に取り掛かる。真っ先に何をしたのか・・。フェアレディZのファイバー製オーバーフェンダーやサニーTSのオーバーフェンダーを、フェンダーに当てて使用できないかを調査開始。結果的にはフェアレディZのオーバーフェンダーを左右逆さまに使うことで、何とか骨格が完成することを見つけ出す。ハンドリベットでオーバーフェンダーを取り付けた上から、アルミ板を板金して少しづつフェンダーを製作。段差を板金用パテで盛り付け修正した。リヤースポイラーは他の車で使用していた物を改造。フロントスポイラーは骨格を角チャンネルで作りアルミ板を整形しアルゴン溶接で仕上げた。レッカー車の積載を考慮して、ワンタッチ留め金(ズースと呼ぶ特殊金具)で簡単に脱着できるようにした車である。この技術は私独特の物であったが、16歳の時に、日産車体で塗装実習を勉強した際の教材からヒントを得ている。この教材は御用済の古いダットサントラックであったが、塗装をするために下地の鉄板まで裸にすると、小さな鉄板が継ぎ接ぎだらけに(溶接)製作されていたのである。もちろん曲線部分のフェンダーも含め、全てのボディーが手作りであった。溶接、板金の基礎技術も学び、転職した整備工場でも板金屋や塗装屋さんの手伝いで更に技術を磨いていたので、日産大森でもTS車両改造なども最初からこなせることができ更に腕を磨くことができた。その腕前を見込まれてのマーチシルエットの話である。手先の器用さは持って生まれた私の長所であったので当時のレーシングカーのゼッケン番号やドライバー氏名の記入は私の担当であった。
このマーチシルエットは「マッチのマーチ」という宣伝文句で、新車販売の広告に一役かうことになりモータショーにも展示され、現在では記念車となって残っている。金色と黒の組み合わせなので、この車を見たことがある人は多いと思う。今度遭遇した際には仔細に観察してみて欲しい。この車は単にカッコばかりでなく本当に富士スピードウェイをマッチ(近藤真彦)がドライブしている。エンジンも改造されTS仕様が搭載されている。この車は、ちょうどマッチがレース活動を開始した時期と重なる。その他、オプション部品開発&組み立て、ラリー&レースサービス(一般ユーザーの修理)、オーテックジャパンではルマン24時間耐久レース用Cカー用VEJ30型エンジン耐久テストをメイン担当することになりベンチテストを繰り返す毎日であった。フルスロットル(アクセル全開)で4800rpmで30分、次は6800rpmで30分と技術員から指示された回転数と時間にのっとってエンジンを連続して耐久試験する。絶えず排気温度、油圧、水温、ブースト圧力、ベンチ内のエンジンからの異音、排気漏れ、オイル漏れ、白煙など監視しながら神経を研ぎ澄まして運転するのである。排気温度は少し油断するとアッという間に1200℃を超える。
また排気管に亀裂が入ったり、排気温度計が壊れたり、ウエストゲートに問題が発生したりするとエンジン回転をアイドリングまで落として(できる限り停止しない)修理し再び実験を続けるという過酷な耐久実験であった。
オーテックジャパン退社後、アタックレーシングを設立。当初は長年の経験を後進の育成に生かそうと日本で初めて「チューニング&メカニック通信教育」を開始し、約3年間で1000名の受講生が受講した。現在も私の教材から基礎を学び、独立してショップを経営しているお店が鹿児島県、兵庫県、埼玉県など何軒か存在している。その後はAE86リビルトミッション、ヘッドチューニング、コンピュターチューニング、テクニカルビデオ製作と新しい分野に次々と挑戦する。
この時までは潤滑系である添加剤や高性能オイルだけで自動車が大きく変わる世界があることなど夢にも思わず、コンピュターチューニングに没頭していた。会社を自分で作ったことでサラリーマン時代では考えられない色々な業者の方と知り合って仲良くなるメリットが生まれた。たまたま小さなオイルメーカーの技術者と仲良くなり、自社ブランドの開発に着手する話が持ち上がる。話をすればするほどオイルのプロは車を熟知しているわけではないことを痛感させられた。いきなりオイルの開発は難しいので、第一段階はオイル添加剤の開発から始めることにする。オイル開発の技術者とはまったく違うスタンスで添加剤をテストすることができるので新しい発見を重ねてゆく。そんな中で今までの長年の経験が生かせることを次第に実感してゆくことになる。やがて潤滑性能を大幅に向上させてゆくと今まで考えられなかった別世界が展開することに驚きの声をあげることになり次第に添加剤とオイルなどの高次元潤滑の世界に引き付けられ没頭してゆくことになる。今までメカニズムに惹きつけられ、真円度、テーパー度、クリアランス、締め付けトルク(トルク締め付け法から始まって、角度+締め付けトルク、ボルト延び測定による締め付け法)だとか、オイル通路拡大、バッフルプレート改造、オイルストレーナーの向きや高さ&吸い込み位置改造、バルブタイミング追及、圧縮比追及、ポート形状追求などを探求してきたつもりだ。コンピュターチューンも一生懸命取り組んできた。でもこの添加剤開発をきっかけに考えてみれば、そこに深く潤滑が関わっていたことを長年にわたって見逃していたことに気づき呆然と佇んでいる自分がいた。
コンピューターチューンを知らない人から見れば、ECUは得体の知れないブラック・ボックスでしかないが、そこにはDATAが存在し、DATAの意味さえ判れば、それを変更することによりエンジンを自由自在にコントロールする(燃料マップ&点火タイミングマップ等、一部のDATAに限定されてしまうが)ことができる。だが、オイルに関しては分析結果で成分の95%が解ったとしても、あまり意味のない世界。残りの5%に性能が隠されている場合もあるし成分で全てが決定されるわけではない。お手軽ECUチューンとは違い、オリジナルオイルなどそう簡単に作れるものではないのである。
性能さえ問わなければAとBを混合しABを作ることは簡単に出来るが、現実問題それだけで高性能化は出来ない。粘度のみを30番と50番を半々に混ぜて40番の粘度を作ることが一番簡単な方法と言える。沢山のDATAもオイル開発になると何の助けにもならないことが多いが、私の場合は様々な経験で培えられたノウハウが後押ししてくれる。
考えてみれば解かることだが、メカニズムから潤滑を担当するオイルを入れ忘れて走行すれば、短時間で焼きついて寿命は終ってしまう。そこを気がつかないで(目を向けないで)長年に渡りメカニズムばかりを追求していた自分に腹が立った。全てのメカニズムは材質、構造、クリアランスというハード部分、それを制御する部分、ハード部分を保護して作用を円滑にするケミカル部分、この三位一体により成立する化学製品なのである。それ以降は液体の性能の重大さに目覚め、現在は液体チューニングに心血を注ぎ、各種潤滑関連製品をリリースするようになった。
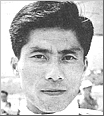 |
日産大森ワークスのチーフドライバー:鈴木誠一選手は私のチューニングの先生でもあった。
誠実・温厚・頭脳明晰な人柄で出張中に一緒にマージャンもした仲であった。 |
日産大森分室に所属していたドライバーは鈴木誠一(富士GCで風戸選手と一緒に事故死・風戸選手がマスコミの注目を集めるが、実績では鈴木誠一選手が多大な業績を残していると私は思っている)、黒澤元治、都平健二、長谷見昌弘が所属していた。びっくりしたのは当時はフェアレディSP310,ブルーバード310、410の頃であるから、オプション部品などほとんどなかった時代なので、自分たちがノーマルピストンを卓上ボール盤で穴を開け、軽量化を施したりコンロッドを軽量加工していたことである。ノーマルのピストンスカートを弓鋸で切断し、ピストンピンの入る肉厚の厚い所を目検討でルーターで削り軽量化を図る。チューニング専門書で「コンロッドをピカピカに研磨して応力分散を図る」と書いてあるが、それはオプション部品が無かったこの頃の話で、ノーマルコンロッドを極限まで細く軽量化の目的で削っていたことが発祥となっている。極限まで細く削れば折れる確率は高まるので、弱い一点に応力を集中させない目的でピカピカに磨いていたわけである。
その当時は、レーシングカーのエンジンや車両の改造第一ポイントは軽量化競争であった。ボディーから必要でない物は全て取り外す。更にホルソーカッターで大きな穴をたくさん開ける。ボンネットはファイバー製に交換する。ガラスはアクリル板に交換。もちろん厳密な規則(レギュレーション)に沿って改造を進める。少しでも違反していれば車両検査で落とされ、出走できないという厳格な規則であった。だからピストンも出来るだけ軽量化を図る。コンロッドもぎりぎり削って軽量化を図る、という時代背景の話が、そのまま現在において常識化してしまっているのである。
その数年後からは強度を高めたオプションコンロッドが発売されるので、コンロッドが強度不足で折れることなど考えられず、折れる場合はコンロッドメタル焼き付きが主原因で折れることになる。オプション・コンロッドはタフトライド加工(高温の曹で、炭素を表面に浸透させ強度アップを図る加工)を施してあるので磨く必要性は無くなり、重量誤差を修正する目的で微調整のみを実施する。表面は固い炭素層が形成されているので、できるだけ研磨はしたくない。だから先に磨いて重量合わせを実施した後で、タフトライド加工を実施する順序が理想的。それから数年後にはNCマシン(DATAをインプットすると自動的に機械加工を連続して行う)が加工現場に採用された結果、H形状の削り出しコンロッドの登場となり、コンロッド重量誤差はほとんど無くなり、コンロッド研磨などレース界では過去の話となってゆく。
それなのにチューニング専門書の本を見ると必ず書いてあるので、この辺の事情を理解していないと、コンロッド研磨に憧れを抱いて実施する。ノーマルコンロッドを研磨して、数グラムの重量合わせを実施しても何の意味も持っていないことに気づく人は少ない。生産ラインではコンロッド重量を自動測定し、一定の幅に揃えて組み込まれるように、生産システムが確立されている。自動車メーカーの技術者はコンロッド重量誤差やピストン重量誤差が性能に与える影響など百も承知なのである。クランクシャフトにしても、あのAE86の4AGエンジンですら10数個のバランス調整穴が開けられ、調整済なのである。そこに1個か2個、浅い調整穴を開けただけで大幅な性能変化が得られるのであれば、当然ながらメーカーは最初から開けてくるのは明らかと知るべきだ。チューニングも時代と共に絶えず進歩してきているのに、実戦経験の無い人の知識では古いノウハウが平気で紹介される。F1を観ていると解かるように毎年毎年、空力ひとつ取り上げても進歩しているのでいつの時代の話か判らないようなチューニングは何の役にも立たないと知るべきだ。もっと言ってしまえば、一戦一戦の戦いの中で絶えず進化してゆく世界なのである。それなのに古い話に戻って技術論を展開しても何の意味も持っていない。同じような現象が最近ではインターネットの世界で存在している。例えば発売当初は安定度が低く、問題も多かった製品が、その後の改良で現在では高い性能を発揮しているのに、インターネットで検索した結果が発売当初の製品に対してのインプレッションだったとしても、見る側はそこまで深く考えないで「この製品は安定しておらず問題が多い」と判断してしまう。また記事自体は新しくとも、それを記載した人の経験が、発売当初のものだけならば、同様なことが起きる。記事を鵜呑みにせず、その信憑性を検証することも大切なことである。
その後も、辻本征一郎、鈴木亜久里、片山右京各選手の車両を担当。この他にも寺西隆利、歳森康師、柳田春人、高橋健二、桑島正美、田村三男、須田すけひろ、萩原光各選手といったプロ選手のメカニックも担当していた。ご存知のように優勝して当たり前の腕の持ち主ばかりであるから、二位になっても「残念!負けてしまった!」と当時は考えていた。私だけでなくドライバーも他のメカニックも同じ気持ちだったと思われる。
フォーミュラーカーは排気量やレギュレーションが色々と変更された中で、F3だけは不変のまま、2000ccエンジンを搭載していた。その代わりとして吸気入り口を小さく絞る規則(リストリクターと呼ばれる吸気制限部品)によってイコールコンデション化を狙っていた。その代償としてエンジン改造はほとんど自由であり、チューナーの腕の見せ所となっていたので私は自分の持てる技術を試す最高の舞台であると考えていた。そんな時勢、大森がNISMOに変わり、F3を走らせることになり私がエンジン主担当として参画することになる。F3シャシーにFJ20を搭載し参戦。ドライバーは鈴木亜久里選手であった。ライバルのトヨタは2TGを途中から軽量型の3SGに変更、最強チームはトムスと戸田レーシングであった。VWは最軽量のエンジンでコックスからの参戦。日産FJ20型はエンジン単体重量が約125kgもあり3SG(約80kg)より約45kg、VW(約75kg)より約50kgも重かった。この重量差はレースの世界だと厳しいハンデとなる。(現GT500で50kgのウェイトハンデは最大)初期開発は追浜特殊車両部(後にNISMO社長に就任した難波社長が率いる部署で、サファリラリー車を開発する部署)が行っていたが、鈴鹿ラップタイムで4秒遅かった。4秒差は走る前から結果が明らかに解かってしまう致命的な性能差であった。しかし、それまで培った技術を駆使し、その後このハンディを跳ね返すことに成功する。
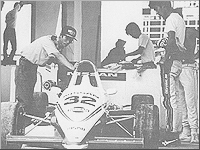 |
マカオGPにて
出走前のエンジン暖機中の藤沢と、それを見守る鈴木亜久里選手。 |
シリンダーブロックをサンダーで一日中削り続けて1日1kgづつ軽量化を図った。全てのボルトは出来るだけ短くカットしワッシャーは使わない。太いボルトは、中をドリルで穴を開け軽量化を施す。少ない予算の中で後半はチタンボルトも採用し、1g単位の軽量化を施していった。富士の高速100Rだと、リアが重いと後部がアウトに流れてしまう。それを解消するためには必然的にリア・スポイラーをライバルより多めに立てることになる。しかし、1ノッチ=5ミリ立てるとパワーの無いF3では、ストレートでのエンジン回転数は300〜500rpmダウンしてしまう。タイムを短縮するための処置がストレートでのタイムを悪化させてしまう致命的問題を抱えていた。だが、5kgのエンジン軽量化が効を奏して100Rでアクセルを全開で踏めるようになり、タイムも0.5秒短縮された。成績も比例するようにアップし、結果はトータル4回の優勝を飾ることができた。(もちろん、これは鈴木亜久里選手のテクニック、シャシーセッティングを請け負ったベテランメカニックの功績でもある)残りの2戦を残す時点でポイントリーダーとなり、マカオGPに招待される。F1ドライバーへの登竜門として有名なサーキットだ。市街地という悪条件とヨーロッパ・トップクラスの車両とドライバーが参戦するマカオGPは、車両とエンジンのポテンシャルが非常に重要であり、歴然たるレベルの差を見せ付けられた。それを一番に感じたのは予選後の車両重量測定。ロールバーにフックを掛け、クレーンで持ち上げる。ワイヤーの途中に重量計をはさんで測定する原始的方式である。理想的重量配分は50:50なので多くのヨーロッパ参加車両は地面と平行に最初から浮かび上がってゆく。我が鈴木亜久里F3車は(ある程度予測できていたが・・・)まずフロント側からゆっくりと持ち上がり、重いエンジン側は一向に地面から離れない。最終的には約45〜50度傾斜した所でようやく全体が浮き上がった。我ながらこれでよく戦っていると妙な感慨が湧き上がってきたことを今でも鮮明に覚えている。ライバルチームやオフィシャルなどのレース関係者からも「よくこんな車でレースを戦っているな」と思わず驚嘆の吐息が洩れていた。この結果を見て、どんな過酷な状況下においてもそれをクリアしようという熱意が結果に繋がり、またそれに自分が組することが出来たことにより、私自身の体の中にそれまでは感じることのできなかった大きな自信が確実に育っていることを強く感じ取ることが出来た。 |
戻る |
|
4−1:沢山の優秀な仲間から吸収して成長できたこと

人間一人の力でも、その力が100%発揮された際には、驚かされるような働きを発揮する。でも時と場合によっては反対に、一人では何も出来ない無力さを痛感させられるときもある。特に災害時などであれば殊更である。日産車体では講師は現場の技術職の人たちで入れ替わりで教えてくれた。その後、転職した整備工場も10人ほどのスタッフがいたが、個性の強いベテラン整備士の技術を盗んで成長できた。板金屋も東京から流れてきた人で優秀な技術を持っていた。昔の腕の良い板金屋は、ドアの板金でもパテはほとんど使わない(下手な人は沢山使っていたが)で、試作車の製作と同じで鉄板を整形して切り貼りしていた。鉄板の凹んだところを叩けば伸びて歪が出て変形してしまう。鉄板を溶接すれば高温で同様に凸凹になってしまう。これを防止するために欠かせない作業が歪取り作業で、アセチレンバーナーで歪の集中する1点を選んで10円玉ほどの大きさに真っ赤に熱する。板金ハンバーで周囲を叩いて、伸びた歪を赤い1点に集める。その後に水で濡らしたウエスで冷却して歪を吸収する。この作業を何十回、何百回と行いながら歪を取ってゆく。1回の歪取り作業を言葉で説明すると長くなるが、実際は短時間に行わないと熱した意味がない。時には数百箇所にこの作業を行う。どこにどのくらいの歪がたまっていて、どのくらいの大きさで幾つやるのかは経験で身につけるしかない高等技術となる。こんな難しい匠の技術はどんなに化学が発達してもロボットマシンでもコンピューター解析(デジタル化)でも安易には達成できないだろう。指先でさぐって鉄板の凸凹やゆがみ具合を探り当てるのも、経験で身につけた匠の技となる。現場作業を一度も経験していない世代は、デジタル化で全てが解析できると思い込んでいる。次第に職人の生き残る現場が減少しているが、一度失われた匠の技は今後二度と復活することは難しい。言わば絶滅危惧種と同じ意味合いを持っている。化学の進歩で得るものも多いが、失う物も多いと痛感させられることは多い。
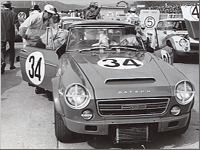 |
第三回日本グランプリ
出走前のパドックに待機中のSR310フェアレディと藤沢。
34番のゼッケンは藤沢が記入した。
当時のワークスカーのゼッケンと選手名は、ほとんどが私が記入していた。 |
日産大森に入社すると、当時のチューニング創世記を模索していたメンバーが集まっていた。鈴木誠一選手は有名な東名自動車(現在は弟の鈴木修二氏が代表)を経営しながら、日産大森ワークスドライバーのチーフドライバーであった。富士GCレースで破竹の連勝を成し遂げた、高原選手のチーフメカニックは大森に在籍していて、その後退職した人が担当していた。そのとき、日産社内や社外から総勢14名が集められ、日産大森分室(ニッサン大森ファクトリー)が誕生するのである。今から当時を振りかって考えると優秀な仲間に刺激を受け、自然と仲間の技術を吸収し自分自身がレベルアップ出来たと感謝している。人によって発想が異なるので一緒に仕事をしていると「エッ、そんな方法もあったのか?」自然と勉強できてしまう。レースは共同作業が多いので、軍隊の規律のように一糸乱れぬ素早い判断力と行動力が常に要求される。そこで言えることは技術的な部分は、外から見える部分と隠された部分と2面があり、内部的部分は実際にそこに在籍し、経験しないと何も解らないということが言えると思う。
たとえば、今まで溶接の経験がない人が溶接を依頼されたとしたら、本屋さんを探し回って専門書を沢山購入して勉強するか、NET検索で情報を収集して作業に挑むだろう。だが最初から綺麗な溶接などできるわけはない。何事も経験しながら身につけてゆくものが技術力という見えない技術なのである。経験を積まないと見えてこない世界は、経験を持たない人から見れば、幽霊と一緒で見えないことばかりで信じられないことになる。溶接ひとつでも材質により溶接方法は異なってくる。一般的な鉄材であればアセチレン溶接や電気溶接、CO2溶接などの方法が用いられるが、溶接方法により使い分けが必要となってくる。材質がアルミニュームに変われば、アルゴンガスを用いたアルゴン溶接でなければできない。溶接でも初心者向きなのがCO2溶接と電気溶接、次がアセチレン溶接で、一番難しいのがアルゴン溶接の順と言えよう。TSサニーのフロントスポイラーは、初期段階ではグラスファイバーが用いられていたが、空力部品は形状や大きさ変更による性能差がダイレクトにラップタイムに影響を与えるため、形状&サイズ変更を実施して性能を追及したい部品である。しかしファイバーだと一度型を起こして製作する工程なので、量産品には向くが性能追及するワンオフ部品には不向きである。そこでアルミ板を加工・溶接してワンオフで製作することになる。私もそれまでアセチレン溶接などの経験があったが、アルゴン溶接は非常に難しかった。息を止めて溶接するわけだが溶接棒の溶ける早さが早いので、右手の人差し指と親指で自動送りで溶接棒を送り込まないといけない。途中で溶接を停止してしまえば、そこが継ぎ目となって連続した綺麗なビートが乱される。また溶接棒ひとつを取り上げても市販品では好みの太さが選択できなかったり、同じように見えるアルミニューム板でも成分の配合により種類があるので、同じ材質の板を切断して好みの溶接棒を自作するように技術レベルはアップしてゆく。更にアルミニュームは熱変化に敏感で熱しやすくさめやすい性質をもつため、溶接開始直後の溶け出しは少なくても溶接が進むにつれて溶け込み量(溶接ビート幅)が大きくなる。そのため、溶接スピードも最初はゆっくりで次第に早くなってしまうが結果として溶接ビートに結果が現れてしまう。ビートを均一に仕上げることはごまかしようがないので至難の技となる。溶接作業に入る前の設計初期段階で、どこをどのように溶接するか、板厚は何ミリにするかといったノウハウも高度に要求される。例えば90度で2枚の板を溶接する場合、普通に両端を合わせて溶接しようとしたらアルゴン溶接では至難の業となってしまう。そこで片側の板の端を数ミリ90度に折り曲げておき、板の切断面と切断面を合わせておき、それを溶接棒を使用しないで溶かしこんで溶接すると、簡単に綺麗な溶接が出来て中味が漏れやすいガソリンでも漏れが少なく信頼性が向上する。このようにまだまだ書ききれないノウハウをたくさん必要とする作業なのである。困難であればあるほど、腕に自信のある人達は競いあって(暗黙の内に)自然と自分たちの技術力を高めていくことに繋がっていった。当時の大森ワークスの戦跡を改めて振り返ってみると、目を見張るほどの素晴らしい結果をたくさん残していることに気づく。このように実際の開発現場の最先端に自分をいつも置いて生きてきた。それはケミカル開発に心血を注いでいる現在でも変わらぬスタンスのままである。 |
戻る |
|
4−2:トラブルの裏には複数の原因が隠されている

自動車の故障と人間の病気とよく似ているという話をした。人間の病気もその人の日常生活、食生活、遺伝など、沢山の要素が複雑に連携しあい、複合で引き起こされる結果と言える。これを自動車に当てはめて考えると・・・
A 日常生活=使用条件
B 食生活=ガソリン(オイル&メンテナンス)
C 遺伝=設計
新車で壊れた場合はC:設計的要因が大半で、後は購入者の誤った使用方法が原因となることが多い。これが中古車になると様相は一変する。ピンときた人もいるようにA+B=結果 図式となるように、Aの使用条件とBのガソリン(オイル&メンテナンス)によって大きな格差が生じてくる。「ノーマル車を改造=壊れやすくなる」と思われがちだが、改造と一言で言っても「良い改造」と「悪い改造」と大きく二つに分けられる。確かに耐久性を悪化させる「悪い改造」を施せば壊れやすくなるが、私が提案している改造は、耐久性も向上し排気ガスも低減できる進歩的改造術である。
5万km、10万km、15万kmと走行距離が増大するほど、故障した際の真の原因追及は難解となる。なぜならどんなに高性能化を図っても、磨耗損傷をゼロには出来ないからである。また部品の材質によっては、経年劣化&変化が避けられない材質も使用されている。オイル交換によってスラッジを含め汚れを外部に排出することになるが、長期間にわたれば人間の歯に蓄積する歯石と同様、汚れ蓄積は避けられない。エンジン部品も毎分、数千回という爆発力が加わっているので、金属疲労が発生し、応力の集中した弱い部分から亀裂が生じたりする。またバルブフェースとバルブシート当り面は、昔はガソリンに添加された鉛で潤滑されていたが、法改正で鉛の使用が禁止されると、ガソリンが無鉛になったため、長期間使用での磨耗は避けられなくなった。これらの複数要因が作用し、バルブ当り面からの圧縮漏れ、ピストンリングとシリンダー当り面からの圧縮漏れが進行してゆく。加えて燃料噴射装置のエアフローセンサーの汚れや磨耗、インジェクターの噴霧状態の悪化など完全燃焼に影響を与える部品の劣化が進行してゆくことになる。
私の勧める、アーシング、トルマリン、コンデンサーチューン、各種添加剤および高性能オイルの使用などは、不完全燃焼に起因するスラッジや燃料希釈発生を抑制する働きを持つので、「正の連鎖」で好調子を長期間維持する補助アイテムとなる。
また、誤認されるトラブルの原因として次のような例がある。例えば8万km走行したATの変速ショックが気になったのでATFに添加剤を添加して様子をみていたら1週間後に走行不能となった。この場合の原因は最後に添加した添加剤に疑惑の目が向けられる。確かに最後に試した物が一番怪しいと疑うのが自然であるが、それ以外にもトラブル発生のトリガーなった部分を考察して欲しい。
確認事項 |
考察 |
メンテナンス記録が残されているか? |
ATF交換の実施状況が判る |
ATF交換は何kmで実施されてきたか? |
ATF銘柄は? |
粘度・特性等が判る |
その人の運転方法は正しいのか? |
信号の度にNや1・2に入れるような運転はATに負担が掛かる |
その車種の平均的AT寿命は? |
車種によりATの設計が違うため寿命は車種ごとに違う |
その車種に多発しているトラブル傾向は? |
特定車種には特定のトラブルが発生する |
添加剤を使用する前の状態は? |
もともと異常があったのか? |
添加剤の市場での評価は? |
効能は広告であり、実際の効果とは限らない |
これらを総合的に判断して初めて解明できてくるものである。ここで走行不能になった一番の要因と思われるのは添加剤の投入以前に、走行距離8万kmということである。AT寿命は80%、場合によっては99%使い果たしていたと考えたほうが自然だと思う。しかし、考察をしなければ「昨日までは正常に動いていたから添加剤が悪い」と思うだろう。同様に車検を終わった車が車検後すぐにパンクすると「車検を受けたのに壊れた。無料で直せ!」という例も同じである。「最後に○○した」という事実があるだけで犯人に仕立て上げられることになる。前出のATの例だと、既に走行距離8万kmは1%も考慮されないで判断されるのである。壊れるまでの1週間と、それまで使用していた8万kmの歳月の違いを少し考えれば誰でも解ることと思うのだが、通常は簡単に無視されてしまう傾向を示す。
添加剤がトリガーとなった可能性:
余談ではあるが、走行不能になった原因に、添加剤を投入したことも要因である可能性は数%と低い確率で考えられる。但しこの場合は、添加剤が悪さをしたのではなく、添加剤が有効に作用したから起きたのである。既に8万キロを走行し、またATFの交換が全く実施されていなければ、ATの中にはスラッジ等の老廃物が蓄積されている。この老廃物を添加剤が洗浄作用によって剥ぎ取った場合、いきなり老廃物がATFの流動経路を塞いでしまう場合も数%と低い確率であるが発生しても不思議ではない。前出の通り、既に8万キロを走行し、寿命は尽きようとしていたのは事実だが、いきなり走行不能になったのにはそんな可能性もあるのだ。
だが、だがらといって添加剤の使用はNGというのは早計である。改善された80%の喜ぶ人がいて、変わらない18%の人、トラブルの発生した2%の人の比率を考慮しなければならない。2%のトラブルを恐れていては80%の良き改善を傍受することはできない。だからこそ手遅れにならないうちの早目の使用を推奨するわけである。
もっと早くATFが交換されていたら・・・・もっと早く添加剤が投入されていれば・・・・きっとスラッジの発生は低減されており、8万キロを超えて性能を発揮していただろう。つまり一番の原因はユーザーの管理方法に問題があったのだ。それを使用した製品に全責任を転換することは的を得ていない。 |
どんな製品にも、設計的な不具合や限度を超えた磨耗損傷を補え切れない限界線は必ず存在する。「添加剤は、どこまでの不具合が完治可能かを明記すべきである」と唱える人を見受けるが、これは作用される部品側の限界点が明確にならない以上明記は不可能である。医者が病気になった人の残り寿命の予測は可能だが、どこまで回復出来るかの判断は難しいという話と似ている。人間の病気ならCTスキャンやレントゲンなどを用いて、内部の進行具合を目でみることが可能であるが、自動車で圧縮圧力を測定したり、シリンダー磨耗損傷をファイバースコープ内視鏡で見ることが出来ても、メタル損傷具合やAT湿式多板クラッチ面の磨耗損傷具合は、分解点検してみないことには解かりはしないのだ。必ずどこかに限界点が存在するように、100%の改善は無理でも、製品Aの故障改善能力が20%、製品Bの故障改善能力が50%、製品Cの故障改善能力が90%とするならば、A&B製品で改善できなくてもC製品なら改善できる可能性が残されている。但し、C製品を使用した人が改善できない10%になってしまうのか改善される90%に該当するかは実施してみる他に調べる方法はない。従って出来るだけ改善能力の高い製品を見つけ出し、状況が悪化する前にテストするのが確実な方法となる。
日ごろからメカに興味がない人ほど、トラブルの症状が悪くなってから相談してくる。健康管理と同じで「症状が軽いうちに対処して欲しい」と願わずにはいられない。対応が早ければ内部損傷は少なくて済むので、修理を望まない人ほど早めの対処と改善能力の高い対策製品(添加剤)の使用が強く望まれる。
マニュアルミッションのギヤ入りが悪くて、シフトチェンジのたびに「ガッン」と大きな音を発生させていると内部のシンクロや、カップリング、ギヤ側面の噛みこむ部分が削れてゆく。新品の時は噛みこみ部分はヤリの穂先のような鋭いV字形状をしているので、V字とV字はスンナリ噛みこむ(正常な状態)。それが何らかの阻害要因によってギヤ入りが悪い車は「ガリッ、ガリッ、」と先端が削られてゆき、次第にV字形状はU字形状に磨耗してしまう。すると最終的にはU字とU字の先端が合致するため、まったくシフトが入らない現象がときどき現れる。この反対に、スンナリ気持ちよくシフトチェンジができる車は、それ以上の走行を経ても、毎シフトでの磨耗が少ないので、消耗は最小限に抑制される。つまり機能が正常に行われていると、メカニズムはいつまでも元気が続き、へたりが少ないことになる。 |
戻る |
|
4−3:最終到達点は液体性能の重要性に着目

昔のレーシングカー(1960年代)で使用していたオイルは、シェルのシングルグレードX-100,#40のみであった。このオイルでTSサニーで8500rpmをまかなっていた。プリンス自動車と合併して解かったことは、スカイラインGT−Rのエンジンとミッション、デフオイルは当然のごとく日産とは違ったオイル銘柄が使用されていた。プリンス関係者のメカニックは「このオイルでないとだめ」と言いきっていたが、その頃はシェルX-100 40番を使用しても壊れないで結果を出すことだけに集中していたので、オイル性能の違いなど眼中にはなかったし、潤滑性能の違いが結果に影響するのは焼きついて壊れることだけと想像していた。潤滑を司る液体性能の重要性に気がつき、開発を始めたのは1990年。考えてみれば30年間の歳月を無駄に過ごしてきたことになる。
 |
TS サニー110 和田孝夫選手の車両も見える |
自動車メカニズムには多くのケミカル(液体)が重要な役割を担って充填されている。
1:エンジン=エンジンオイル
2:AT=ATF CVT=CVTF
3:MT=ミッションオイル
4:パワステ=パワステフルード
5:デフ=デフオイル
6:エアコン=エアコン用オイル
7:ブレーキ=ブレーキフルード
8:ラジエター=LLC
9:バッテリー=バッテリー液
10:その他AYCやトランスファー等
メカニズムは、このように実に様々なケミカルが充填されて初めて機能するように設計されている。まず一般的に考えることは・・・
1:レベルは適切であるか点検する。
2:汚れたり劣化していないかを確認し、交換時期を検討する。
3:交換する際に、どこの製品を使用するか検討する。
自動車愛好家の関心時は、「少しでも車両の性能をアップしたいしたい」という事。その目的は各個人で異なってくる。
1:少しでも燃費向上を図りたい人。
2:少しでも走りのポテンシャルを向上したい人。
3:マニュアルミッションのギヤ入りの渋さなどの欠点を改善したい人。
4:自動車の耐久性を高め、長期間にわたり使用したいと考える人。
しかしながら、現実的には「予算内で・・・」でと注釈が付く。従って、どんなに高性能な製品が存在しようとも、価格的に手が届かなければ、それを理由に使用する機会は永遠に訪れない。結果として、液体の性能により車両のポテンシャルを高めることが出来ることに、気が付かないで終わってしまうのである。実際、車両の販売・修理・再販に携わる人や、潤滑製品を最も多く販売するGS・用品店などでも同様である。それはハイ・ポテンシャルな製品を実際に経験してみて初めて解ることであり、どんなに人から話を聞かされたとしても、にわかには信じられない世界だからである。現に、私自身、この事実に直面するまでは信じていなかったし、逆にその事実に直面したからこそ、添加剤やオイルをチューニングの要として考えるようになったのである。確かにメカチューンに於いてもコンピュターチューニングでも車の走りを変えることは出来た。だがケミカルによる性能アップは、単純に速さだけを向上させるのではなく、走りの味そのもものまで別物に変えてしまう。この「走りの味」という表現は抽象的だが、具体的には、車両が自分の「意図通りに反応してくれる結果から得られる爽快感」と考えてもらえればよいと思う。シフトチェンジの度にシフトに気を使ったり、踏み込んでもリニアに追従しないエンジンではこの爽快感は得られない。人馬一体の如く、「人車一体」となり、「車両」であることを意識しない走行感覚である。多くのメカニズムは潤滑性能を高めてゆけば、更に高い性能が引き出せることが解ってきた。タイトルでは「液体性能の重要性」と謳っているが、単純な潤滑性能向上だけでなく「摩擦と滑り」という相反する要素が、相乗的に作用を齎すということ。それはオイルの潤滑性能が、燃焼の高効率を促し、結果として振動やトルク、馬力、レスポンスなどに良い影響を与えるだけでなく、全く液体として繋がっていない「ミッションの入り」にさえも深く関与していることでも判る。当然、メカニズムの寿命にも大きく影響している。(これらの詳しい解説は他の項目で詳しく述べる)
エンジン内部の構造が理解できてくれば、そこから「エンジンはオイルによって保護されて性能を発揮している」ということが理解出来てくる。その場合、次のステップとして「保護性能を高め自動車の耐久性を高める」に到達し、最終的に「オイル性能によってエンジン性能も耐久性も大きく左右される」という結論に到達する。だが実際にはその上のステップも存在する。しかしながら残念なことに、それをここで私がいくら語っても理解することは出来ないだろう。「百聞は一見にしかず」と言うが、こればかりは実際に自分で経験しなければ、永遠に私の話が玉虫色にしか見えないからである。
ブレーキフルードに関しても同様で、液体性能がブレーキ自体に重要な役割を果たす。サーキット走行を行う人なら経験がある筈だが、ブレーキフルードを沸点の高いDOT4とかDOT5に交換する。すると対温度特性は優れるのだが持続性が低くなる。つまり、「フルードを交換するとブレーキが変わる」という結果の先に「フルードを改良すればブレーキが変わる」という発想に到達できることになる。こうして[ブレーキフルード添加剤]という発想が生まれた。ブレーキフルードの場合は潤滑ではなく「圧力を効率良く伝達する」性能が重要となるが「液体性能」を高めることによりパフォーマンスが向上することには変わりない。
時代が進むにつれ「常識めいた迷信」を唱える人も減少傾向にある。自分の常識だけで判断し、最初から試行することを否定していれば、永遠にその存在さえ気がつかない。20年前30年前の私自身がそうであったと同じように・・。 |
戻る |